Fasteners and Machining: Key to Efficient and Dependable Production
Navigating the Globe of Fasteners and Machining: Techniques for Accuracy and Rate
In the complex realm of fasteners and machining, the mission for accuracy and rate is a continuous difficulty that requires meticulous interest to information and strategic preparation. From understanding the diverse selection of fastener types to choosing optimum materials that can stand up to extensive needs, each action in the process plays an essential duty in achieving the wanted outcome. Precision machining techniques even more boost the complexity of this craft, calling for a delicate balance between technological competence and innovative strategies. As we look into the methods that can boost both rate and efficiency in this domain, the interplay between high quality control actions and operational excellence becomes a critical centerpiece.
Understanding Fastener Types
When selecting bolts for a project, comprehending the numerous kinds readily available is vital for making certain optimal efficiency and dependability. Screws are used with nuts to hold products with each other, while screws are flexible fasteners that can be used with or without a nut, depending on the application. Washing machines are crucial for dispersing the load of the bolt and avoiding damage to the product being secured.
Choosing the Right Materials
Comprehending the importance of picking the appropriate products is paramount in making certain the ideal efficiency and integrity of the chosen fastener types talked about formerly. When it involves bolts and machining applications, the material option plays a critical function in identifying the general toughness, toughness, corrosion resistance, and compatibility with the desired setting. Various materials offer differing properties that can significantly influence the performance of the fasteners.
Typical materials made use of for fasteners consist of steel, stainless steel, brass, titanium, and aluminum, each having its special strengths and weaknesses. Steel is renowned for its high strength and durability, making it ideal for a broad array of applications. Selecting the appropriate material includes thinking about elements such as toughness requirements, environmental problems, and budget restraints to ensure the preferred efficiency and durability of the bolts.
Precision Machining Techniques

Along with CNC machining, other precision strategies like grinding, turning, milling, and boring play important functions in fastener manufacturing. Grinding assists attain fine surface coatings and have a peek here tight dimensional tolerances, while turning is often utilized to develop cylindrical elements with specific diameters. Milling and boring procedures are essential for shaping and creating holes in bolts, guaranteeing they meet exact specs and feature correctly.
Enhancing Speed and Effectiveness
To enhance fastener manufacturing processes, it is necessary to simplify operations and execute effective approaches that enhance accuracy machining strategies. One vital strategy for improving speed and effectiveness is the application of lean production concepts. By lowering waste and concentrating on constant renovation, lean techniques aid eliminate bottlenecks and optimize operations. Furthermore, spending in automation modern technologies can significantly boost production speed. Automated systems can handle repetitive jobs with accuracy and rate, enabling workers to concentrate on more complicated and value-added tasks. Embracing Just-In-Time (JIT) inventory management can likewise enhance efficiency by making sure that the ideal materials are available at the correct time, reducing excess inventory and decreasing preparations. Promoting a culture of partnership and communication amongst team members can boost general efficiency by advertising transparency, analytic, and innovation. By incorporating these methods, producers can attain a balance between rate and precision, eventually improving their affordable side in the read this article bolt industry.
Quality Control Procedures
Implementing extensive quality assurance actions is important in ensuring the reliability and consistency of bolt items in the manufacturing process. Quality assurance steps include numerous phases, beginning with the selection of resources to the last examination of the finished fasteners. One essential facet of quality assurance is carrying out detailed material inspections to validate conformity with specifications. This involves evaluating aspects such as material strength, composition, and resilience to ensure that the fasteners meet industry criteria. Additionally, checking the machining refines is necessary to copyright dimensional precision and surface finish top quality. Making use of advanced technology, such as automated examination systems and accuracy measuring tools, can enhance the precision and performance of quality assurance procedures.
Regular calibration of devices and equipment is necessary to maintain consistency in manufacturing and guarantee that bolts satisfy the required resistances. Carrying out strict procedures for recognizing and dealing with problems or non-conformities is important in protecting against substandard products from entering the market. By developing click to read more a comprehensive quality assurance structure, suppliers can maintain the reputation of their brand and provide fasteners that fulfill the greatest standards of performance and sturdiness.
Conclusion
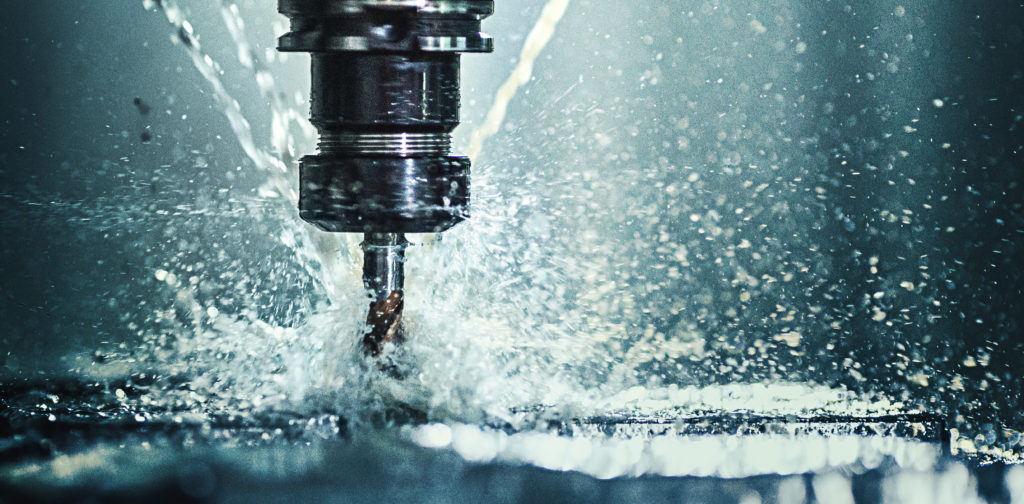
In the complex world of bolts and machining, the mission for accuracy and rate is a continuous difficulty that requires careful focus to information and critical preparation. When it comes to bolts and machining applications, the material option plays an important function in figuring out the total stamina, durability, deterioration resistance, and compatibility with the designated atmosphere. Precision machining includes various sophisticated methods that ensure the limited tolerances and specs required for bolts.In enhancement to CNC machining, other precision strategies like grinding, transforming, milling, and boring play important roles in bolt manufacturing.To enhance fastener manufacturing procedures, it is necessary to enhance operations and implement reliable methods that complement accuracy machining methods.